Situation This client was firing up gas burners to bring chemical baths up to temperature without any monitoring. When operators arrived in the morning they immediately fired up burners. Burners were not turned off until the very end of the workday. Often bath temperatures were higher than required. Process Improvements CMI technology was implemented to…
Read more
Energy Cost Reduction
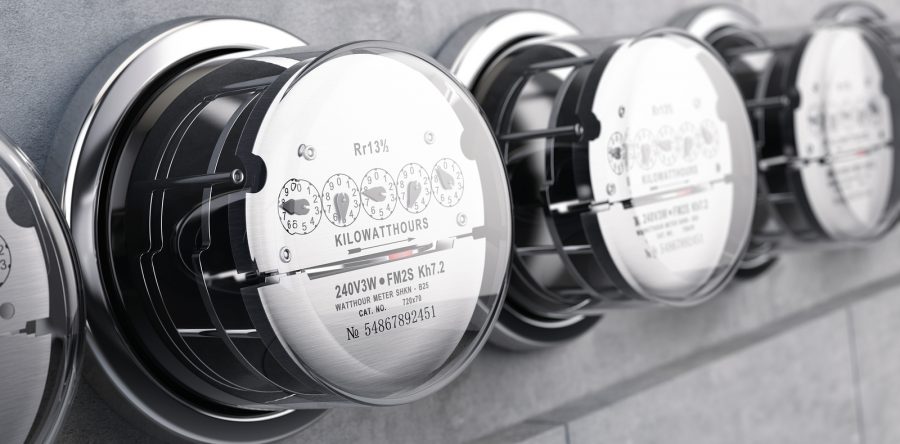
admin
admin
admin